Shanghai--(Business Wire)--Henkel has opened theNVH Lablocated in the HenkelAdhesive Innovation Centerin Shanghai, China.The 400sqm facility will help the company tostay on top of automotive trendsand offer cutting-edge OEM solutions to meet the evolving and challenging requirements in the area of NVH.
Both noise and vibration play a crucial role in the perspectiveof vehicle quality. Automotive engineers are highly prioritizing development of designs and new materials to eliminate or reduce noise sources and optimize transmission paths to the occupants. As a result of increased competition, automotive OEMsare pressured to developvehicles with competitive NVH performance in shorter design cyclesforlowerdevelopment and vehiclecosts.
Henkel has a long history of providing NVH solutions to the automotive industry and has established itself as apreferred supplier to OEMsworldwide. Teams located in key design centers have been helpingcustomersidentify and solve NVH problems globally.
Henkel has broad capabilities in noise/vibration measurement, providing technical service in accordance with international test standards and by customized procedures. The new NVH Lab is dedicated to noise regulation testing and NVH quality improvement, with itsstate-of-the-art experimental and computational analysis facilities. The test lab features a fullcar body oven, a 3D printer, Liquid Applied Sound Deadener (LASD) spray equipment,a mode test platform, a laser vibrometer, and anechoic roomsthat are used to test vehicle NVH performance. For LASD and HDF new damping concept application, the latest test lab system, pulse analysis software and optical measuring systems are also used to evaluate the vibro-acoustic performance of subsystem and vehicle level. The whole engineering chain fromsimulation, spray, baking to validation can be done in the lab to meet OEMs’ quick response requirements &shortened DVP period. For structural reinforcement parts and pillar filler, Henkel can provide industrial prototypes manufactured by the 3D production system for line trial and through APQP process, furthervalidate special sealing performance DVP&R with body leakage tester for vehicle and baffle parts.Experienced automotive engineersare ready to serve customers with CAE simulation, part analysis, design and modification in addition to producing samples for validation purpose and computing energy efficiency.
Traditionally, Henkel engineers have hand-built their own prototype OEM vehicle pieces or contracted injection molding shops to build prototypes. However, there are limitations in hand-fashioning metal auto-body pieces, and injection molding can add weeks and significant cost to a project. Henkel’s 3D printer allows the labto go from CAD rendering to prototype part within hours, dramatically shaving time off the design process. The 3D printer fabricates prototype parts using a production-grade thermoplastic that can tolerate chemical treatments, impacts, and withstand the high temperature e-coat baking, allowing for more vigorous testing that better matches the customer requirements.
This new technology allows Henkel greater agility in serving customer needs and helps the design verification and prove-out process move significantly faster. Eric Aldstadt, Henkel’s Acoustic & StructuralBusiness Director of Asia Pacific, confirmed that the 3D printer builds more than rapid prototypes; it helps build stronger relationships with customers. “A concept that started as a whiteboard sketch can be quickly turned into a representative, physical part engineers can touch and feel. And, they can physically review Henkel’s part solution withtheir cross-functional team. A picture may be worth a thousand words, but the ability to hand our customer a physical part is truly top-notch engineering support. Henkel’s ability to manufacture three-dimensional prototypes in one day solidifies our commitment to putting customers at the center of what we do.”
NVHrefinement has become an essential vehicle development attribute.Withglobal expertise based on extensive experience in theautomotivemarket, Henkel is positionedto provide sustainable, innovative and efficient solutionsacross the entirevalue chain. Henkel’s NVH solutions allow the OEMs and automotive suppliers to experiment with ways of damping the noise and reducing weight at the same time to maximize efficacy in all areas involving automotive adhesives.
Contacts:
Henkel
Business Development Manager
Brian Tong, +86 21 2891 8874
Marketing Communication Manager
Echo Liu, + 86.21.28915832
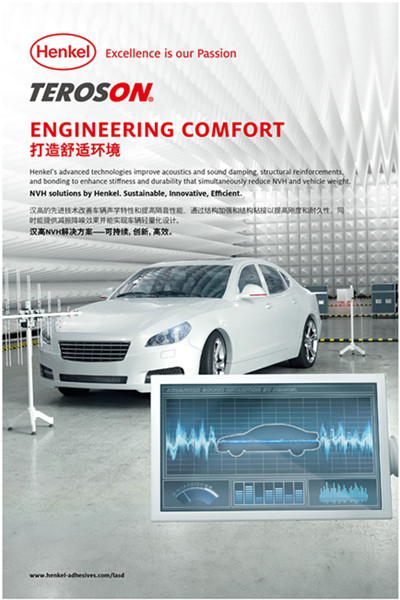
Henkel provides NVH solution to the automotive industry